Tool Steel CNC Machining
Tool steel is a durable, high hardness, high wear resistance and deformation resistance steel material used to make cutting tools, gauges, dies and wear resistant tools.
With 17 years of manufacturing experience in tool steel CNC machining, we have an in-depth understanding of the unique challenges of working with this material. You don't have to worry about machining this hard metal, Tuofa offers a range of services from product design to prototype development, both for individual parts and batches. Immediately review Tuofa's expertise in tool steel machining and learn how we can help you succeed in the process.
Type of Tool Steel
Classification of steel for tooling The tool steel is classified into six types including: water-hardening, cold-work, shock-resisting, high-speed, hot-work, and special purpose. The choice is determined by the needs like price, operating temperature, desired hardness of the surface the strength, resilience to shock and toughness.. The more extreme the conditions of service (higher temperatures, abrasiveness and corrosion, greater load) the higher the alloy content, and consequently the carbide content needed to make the tool steel.
AISI and SAE in the United States classify tool steels
Defining property | AISI-SAE grade | Significant characteristics |
Water-hardening | W | |
Cold-working | O | Oil-hardening |
A | Air-hardening;medium alloy | |
D | High carbon;high chromium | |
Shock resisting | S | |
High speed | T | Tungsten base |
M | Molvbdenum base | |
Hot-working | H |
H1-H19: chromium base H20-H39: tungsten base H40-H59: molybdenum base |
Plastic mold | P | |
Specialpurpose | L | Low alloy |
F | Carbon tungster |
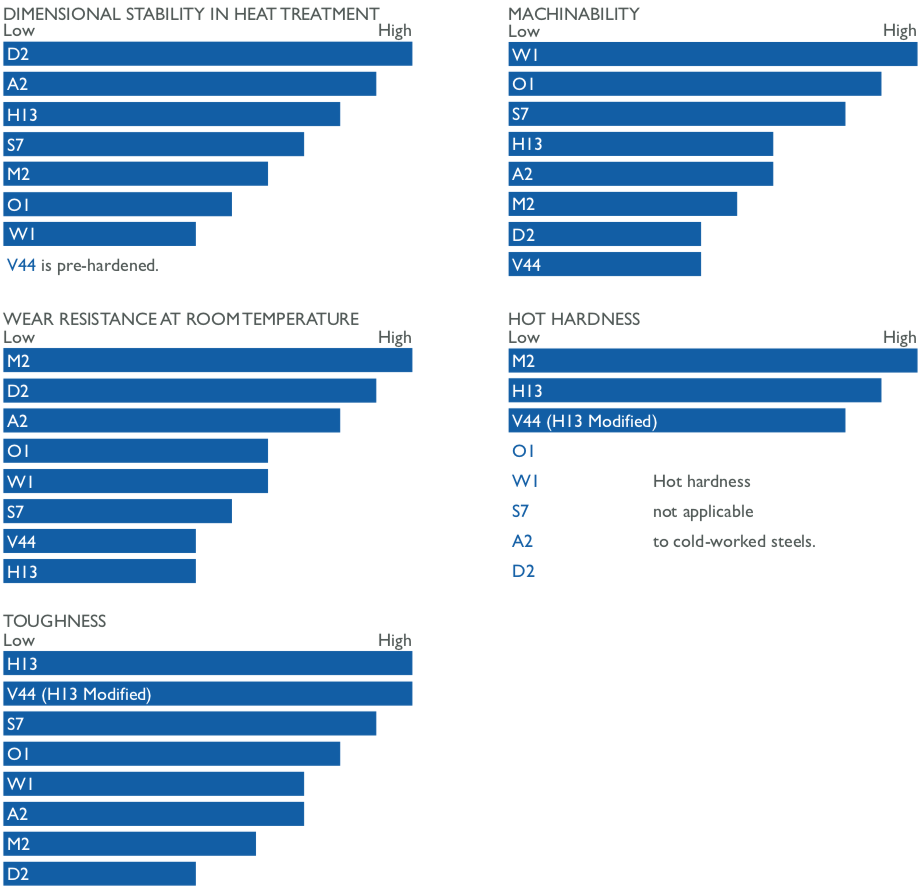
Water Hardening Tool Steel Machinability
Water hardening steel: that are water-hardened contain 0.6%-1.4 percent carbon and are very low alloyed to allow simple machining or for forming. Its hardenability is very low and therefore W steel has to be quenched rapidly with water in order to achieve the desired hardness. This is why it is sometimes referred to as water-hardening steel.
They are suitable for lower temperatures, like knocking, cold heading, taps, stamping and more. If the temperature is greater than 150degC it starts to shrink, which is why it is recommended to use small parts that work under 150 degrees Celsius.
Due to its excessive carbon, the material is able to be used without additional heating treatment. The highest achievable Rockwell the hardness of HRC57 to HRC60. Its melting point is 1538°C it's yield strength ranges from between 380 and 690 Mpa. W1 can be utilized to make manual metal cutting tools such as drill bits, cold-heading embossed taps, drill pipes, reamers mechanical keys that are high-strength and bushings.
O1 Tool Steel Machinability
O1 Tool steel is an oil-hardened general-purpose steel cold-worked with excellent hardness and wear resistance. It has easy to machine properties and a lower heat of hardening as compared to other grades. after tempering and hardening, it is extremely stable and does not suffer from deformation. (but A2 is a good choice for situations where greater dimensional stability may be needed during the process of the process of hardening). The highest Rockwell strength that O1 tool steel from has the ability to attain is HRC57-HRC62.
The melting temperature is 1538 degrees Celsius, with a yield strength of 345Mpa-682Mpa. Some common applications for O1 tool steel include: bending dies, piercers, broaches, blanking dies, forming dies, gauges, cutting dies, bushings, knives, drawing dies, etc. Also , it makes great cutlery.
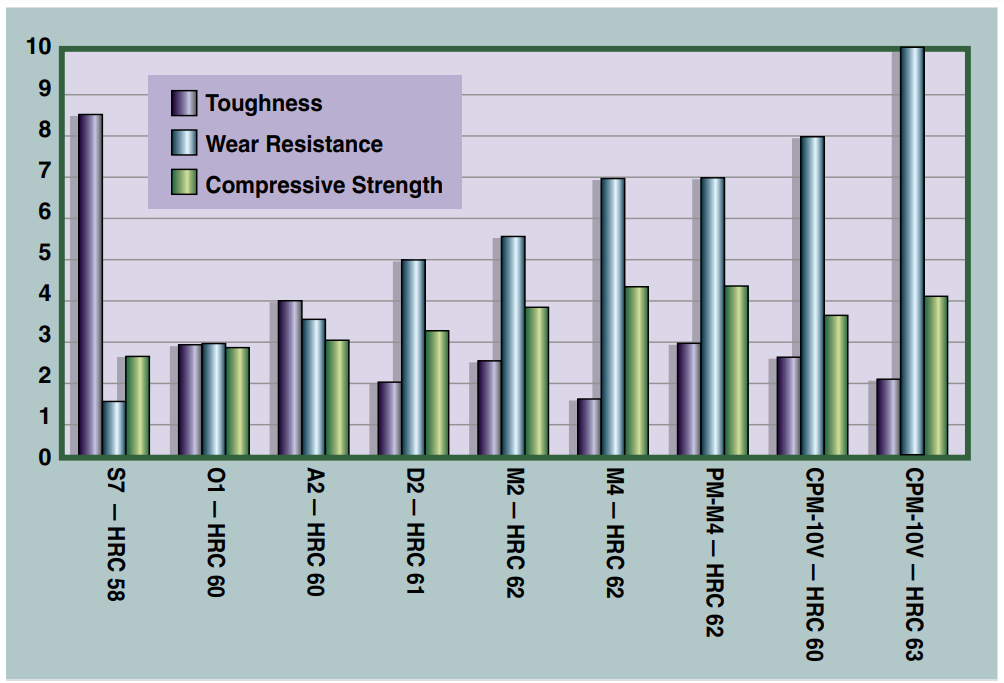
Try Tuofa Now!
Hard metal machining is something that many manufacturers find troublesome, but for Tuofa, our tool steel machining machinists produce flawless parts that meet or exceed industry standards.
A2 Tool Steel Machinability
A2 Tool Steel is an air-hardening cold-work steel which is more superior to O1 tool steel for applications that require more dimensions stability, machinability in addition to safe hardening. The wear resistance and cost is comparable to D2 and O1 tool steels.
The melting point that can be achieved for A2 steel is 1438degC , and its yield strength is 745Mpa. It is utilized in situations in which wear resistance is crucial like cutting dies for blanking, tools and trimming dies, stamping dies, embossing, drawing dies, and various dies, such as extrusions as well as punches and shearing blades, slitting blades and gauges, knurling instruments, gauges as well as mandrels, rolls and machine parts,.
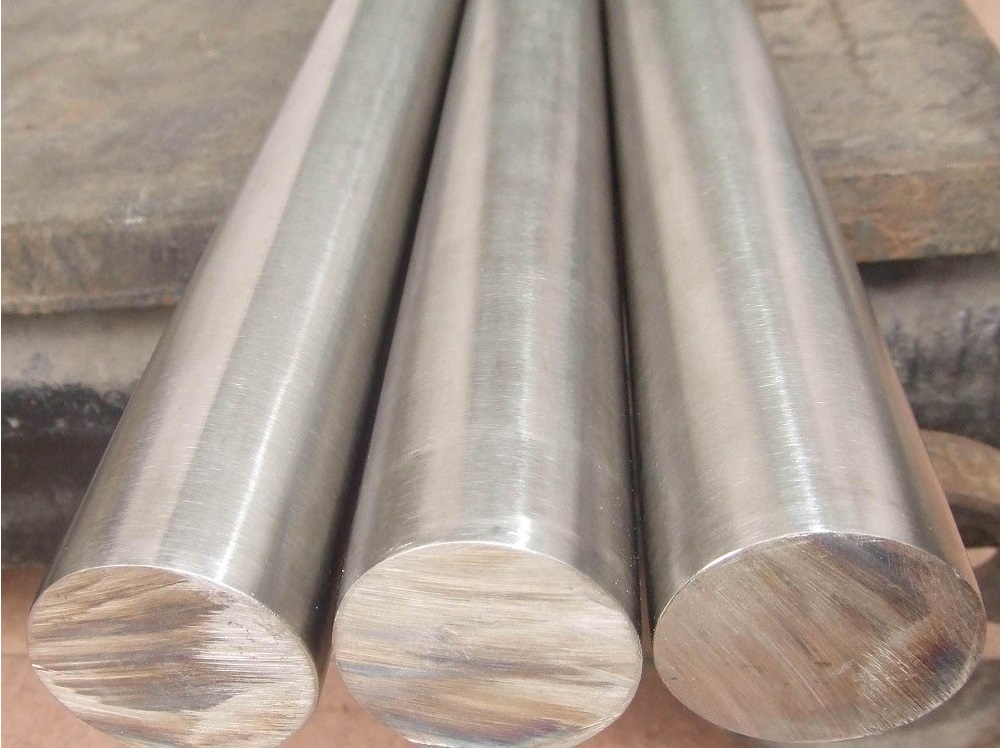
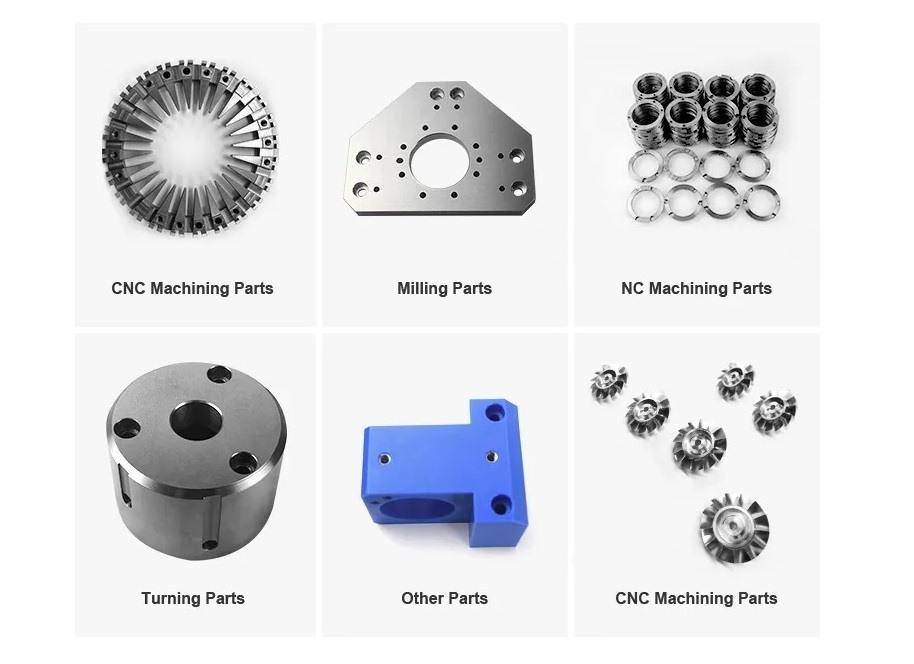
D2 Tool Steel Machinability
D2 steel is a type of an air-hardened high-carbon cold-worked, high-chromium steel, which is an extremely high resistance to wear.
The highest Rockwell the hardness D2 steel is HRC62-C65. The melting temperature is 1385 degrees Celsius, and yield strength is 765 Mpa. D2 steel's ability to deep harden can help prevent cracking and chipping. These attributes, together with the cost are what make D2 tool steel an excellent selection for long-cycle tooling processes that require maximum heat-treatment durability, dimensional stability, and resistance to wear, like Thread rolling tools, laminated dies blanking dies, molding dies, trimming molds embossing tools, drawing tools extrusion dies, etc
People Also Ask
Is tool steel easy to machine?
O1 tool steel is a general tool steel and also a low alloy cold work tool steel. Composed of chromium, manganese, and tungsten, O1 tool steels are relatively inexpensive to machine. |